In the food industry, maintaining consistent product weight is crucial for quality control, regulatory compliance, and cost efficiency. This is where weight checker machines (also known as checkweighers or weight inspection systems) play a vital role.
This article explores:
✔ What a weight checker machine is
✔ How it works
✔ Key benefits in food packaging
✔ Different types of checkweighers
✔ How to choose the right one for your production line
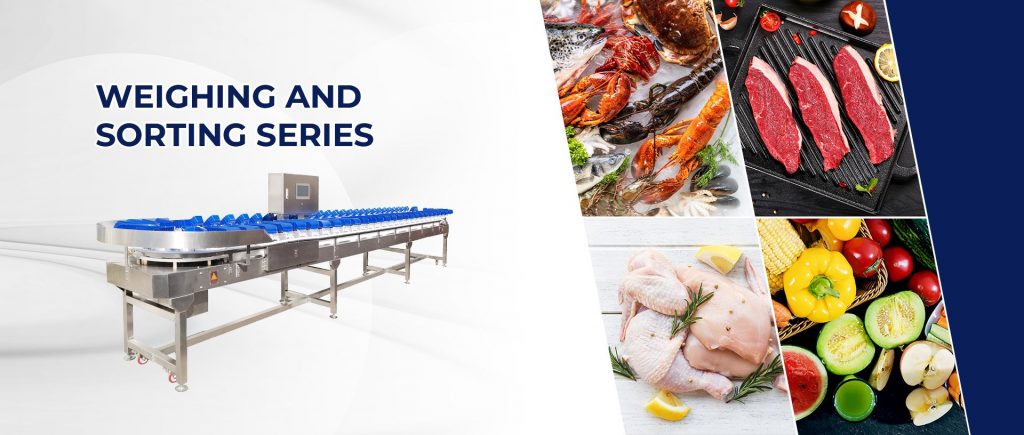
What Is a Weight Checker Machine?
A weight checker machine is an automated system that precisely measures the weight of productson a production line. It ensures each item meets predefined weight limits, rejecting underweight or overweight products to maintain consistency.
Common Industries Using Weight Checkers:
- Food & Beverage (snacks, meat, dairy, frozen foods)
- Pharmaceuticals (pill counting, bottle filling)
- Cosmetics & Chemicals (tubes, bottles, pouches)
- Logistics & E-commerce (parcel weight verification)
How Does a Weight Checker Machine Work?
A typical weight inspection system follows these steps:
- Product Entry → Items move onto a conveyor belt or weighing platform.
- Dynamic Weighing → Sensors measure weight while in motion (high-speed lines) or at a stop (precision checks).
- Data Comparison → Compares weight against preset tolerances.
- Accept/Reject Decision → Passes compliant items, removes outliers (via air blast, pusher arm, or diverter).
- Data Logging → Records weights for quality reports (useful for FDA, ISO, or retail compliance).
Key Components:
- Load cells (high-precision sensors)
- Rejection mechanism (air jets, arms, or flaps)
- HMI (Human-Machine Interface) for settings adjustment
- Software integration (ERP, SCADA, or QA systems)
5 Ways Weight Checkers Improve Food Packaging Efficiency
1. Ensures Compliance with Regulations
- Avoids fines from regulatory bodies (FDA, EU standards) by ensuring accurate labeling.
- Prevents customer complaints due to underfilled packages.
2. Reduces Product Giveaway & Waste
- Overfilling costs money (e.g., a 1g excess per snack bag = tons of wasted product yearly).
- Rejects underweight items before they reach customers.
3. Increases Production Line Speed
- Modern checkweighers process up to 800 items per minute without slowing packaging.
- Replaces manual checks, reducing labor costs.
4. Enhances Quality Control
- Detects missing components (e.g., a missing sauce packet in a meal box).
- Identifies machine errors (like inconsistent filling).
5. Provides Data for Process Optimization
- Tracks trends (e.g., “10% of products are 0.5g underweight at Station 3”).
- Helps adjust filling machines for long-term consistency.
Types of Weight Checker Machines
Type | Best For | Speed | Accuracy |
---|---|---|---|
In-Motion Checkweighers | High-speed lines (snacks, bottles) | 100-800/min | ±0.1-1g |
Static Weighing Scales | Small batches, high precision (pharma) | 20-100/min | ±0.01g |
Combination Weighers | Irregular items (vegetables, nuts) | 50-120/min | ±0.5g |
Multihead Weighers | Granular products (cereal, candy) | 100-300/min | ±0.2g |
How to Choose the Right Weight Checker?
Consider these factors:
✔ Product Type (solid, liquid, fragile?)
✔ Production Speed (items per minute)
✔ Required Accuracy (±0.1g vs. ±1g)
✔ Integration Needs (ERP, reject mechanisms)
✔ Budget (entry-level vs. high-end systems)
Pro Tip: Request a free trial or demo from suppliers to test performance.
Conclusion
A weight checker machine is a must-have for food manufacturers aiming for efficiency, compliance, and waste reduction. By automating weight inspection, businesses save costs, improve quality, and meet industry standards seamlessly.
Need a Weight Checker for Your Line?
Contact Us for expert recommendations tailored to your production needs!
原创文章,作者:admin,如若转载,请注明出处:https://www.foodequip.net/42